Table Of Content

Once built, ICF homes are indistinguishable from their traditionally-framed counterparts. ICF assembly is easy if you know what you’re doing—In practice, it’s relatively simple to stack ICFs into walls, although bracing and leveling before the pour are critical. Each system goes together a little differently, so the manufacturer’s instructions are a must-read before you start. Just like bricks or concrete masonry units, the first course sets the tone for the rest of the installation, so extra attention at the beginning will pay off. Cuts in the forms can make the concrete pour more shaky; avoid cutting corner blocks, use plenty of bracing, and secure large joints with scabs of plywood. ICFs have a relatively low R-value—Concrete has virtually no insulating value — just R-0.08 per inch.
What is the Maximum R-Value of an ICF Wall?
The key is the hollow space in between the foam walls of the forms. As the forms are placed in the appropriate configuration to create the walls of the home, concrete is poured inside and left to set. This bonds the forms together and creates contiguous walls throughout the structure. Insulated Concrete Forms (ICF) are becoming a more common way to build homes. This innovative building material is typically made of blocks of polystyrene foam with space in between to pour a concrete wall.
Intermediate Care Facility Program Types (ICF/DD, ICF/DD-H, ICF/DD-N*)
As a result, homes built with ICFs offer roughly a 70% noise reduction compared to an average home. Vertical steel is placed before each pour and if the structure above is a continuation of ICFs, then a cold joint dowel would be placed to tie the next pour to the first. Most bracing systems have adjusting turnbuckles which allow the walls to be perfectly straightened as the pour is finished. Also, most companies offer training and technical support in addition to providing installer manuals, pre-engineered tables, CAD details, and engineering models. Appendix J regulates the repair, renovation, alteration, and reconstruction of existing buildings and is intended to encourage their continued safe use.
Plan: #153-1379
This 2 bedroom, 3 bathroom home plan is 50″ x 30″ and features an ICF (Insulated Concrete Form) foundation. The home includes a kitchen, living room, office, and garage along with 2 bedrooms and 3 baths. This home plan is perfect for those who are looking for an energy-efficient home that is also stylish and modern. This 60″ x 60″ Modern ICF House Plan is the perfect choice for those who are looking for a home that offers plenty of space and all the modern amenities. The home features 4 bedrooms, 4 baths, a kitchen, a dining room, a living room, a shop, a covered porch, a garage, and a multi-purpose room. With all of these features, this home is sure to meet the needs of any family.
DOE ZERH 2013 Case Study: e2 Homes Winter Park, Florida [2-page summary version]
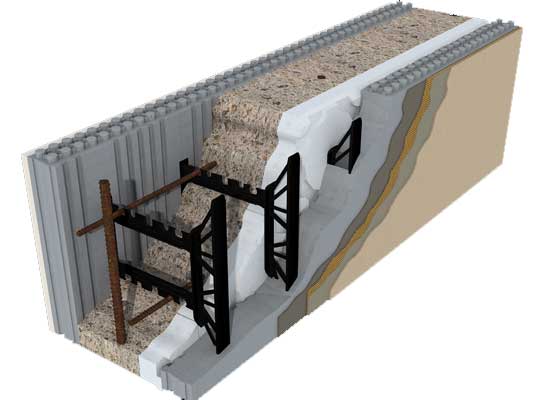
Concrete block home designs use CMUs (concrete masonry units) as the primary material for construction. As mentioned previously, ICF forms cost an average of $3.50 to $4.00 per square foot. Once you factor in additional costs like concrete, rebar, hardware, labor, and more, the average total cost using ICF forms is around 15-20% more than traditional stud framing.
Plan: #175-1117
One of the most appealing aspects of using insulated concrete forms is that it has the potential to significantly reduce the heating and cooling costs of a particular building. That’s also the most impressive feature of ICF walls; they can release heat in the summer and store heat in the winter. In some instances, ICFs are estimated to save about 20% of total energy costs.
Year-Round Building
So, the time savings can be significant, depending on the design of the home. If you are interested in upgrading the walls of a particular building or space and are considering insulated concrete forms, here are a few pros and cons that you should consider before constructing. A cost-effective option, insulated concrete form houses are engineered to handle significantly greater loads than concrete masonry unit (CMU) houses. Able to span distances and support weights that would otherwise require big steel or concrete columns, ICF walls speed up construction time, create a safer work environment, and require fewer workers. A single ICF form is equal in size to 6 CMU blocks, as well as lighter, quicker to stack, and already insulated. ICF buildings are constructed using a running bond interlocking manner with the most common size of 4 foot long and 16 inch high blocks.
Our service area is Pinellas County Florida with focus on building FEMA compliant & hurricane resistant custom homes. Helping you find your dream home, Gast Homes can select the best matches or create a completely new design that incorporates your tastes and preferences. Offering 30+ ICF plans, including hard-to-find coastal elevated homes, ranches, two-stories, and condos, our team will help you determine what features in a home plan are important to you. Incredibly, the cost of living in an ICF home is no higher—and may be cheaper—than living in a regular house.
Plan 4300
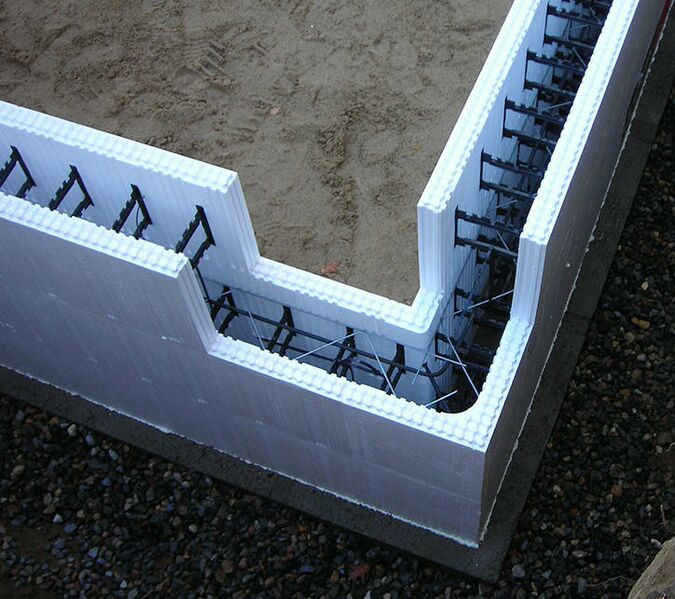
These “reversible” forms save time during placement and prevent improper alignment. Special units for corners, floors, and roof assemblies round out the product lines and improve the engineering of the system and energy efficiency of the final construction. Insulating concrete forms provide benefits to builders and building owners alike. When comparing the impact resistance of concrete walls to conventionally framed walls, concrete walls are more effective at stopping debris. Demonstrating their strength, ICF walls easily resist wind-driven debris. In simple terms, ICF construction generally cuts energy bills in half.
The forms we used to build our house consisted of two layers of insulating foam approximately 2 inches thick, inside and out. The Insulated Concrete Blocks measure roughly 16 inches tall by four feet long by 12 inches wide. They have an inner and outer plastic framework in the forms that stabilizes the form and provides strips that can be drilled into to mount drywall, cabinets, wood trim, and siding on the outside. ICF (Insulated Concrete Forms) are premade forms that fit together like legos or large interlocking blocks. During construction, the ICF blocks are fitted together, laced with rebar, and filled with concrete.
Walls and openings must be well braced to maintain structural integrity. You only get one chance to pour it right and it can’t be adjusted after the fact. Dedicated ICF builders have specialized braces for this purpose, and know how to work with the forms to avoid problems. Too thick, and you’ll end up with air pockets in the wall because the cement has trouble filling the forms completely. About the only thing that is a little tricky is hanging things on the exterior walls, because there are no studs and the stripping is hard to find under the paint and drywall.
Habitat For Humanity of Long Island building its first concrete home - Riverhead News Review - Riverhead News Review
Habitat For Humanity of Long Island building its first concrete home - Riverhead News Review.
Posted: Fri, 08 Dec 2023 08:00:00 GMT [source]
Thankfully, both California homeowners and the California government are known for demanding innovation and advancement in the residential construction industry. Because of this, it is possible for California homeowners to find builders with ICF construction experience. As one of California’s premier design-build firms, Element is one such resource. Speaking with Rene Latosa -- a Santa Rosa resident who lost his home in the Tubbs Fire --, Turner and Gould explain why California homeowners have adopted ICF. Quoting Latosa, they write that “‘the fire safety [of ICF homes] is almost 100%, the durability is 1,000 years.’” Because of this, homeowners have turned to ICF in the rebuilding process. If a fire is started within the home, the fire-resistant concrete and foam of exterior walls will not prevent the spread of flames or smoke indoors.
Knowing that they planned to live there for at least 15 to 20 years, the owners recognized early in the process that they wanted the home to have energy efficiency, quality, and permanence. They determined insulating concrete form (ICF) walls provided the best performance for their needs. An ICF house costs around 4-7% more to build than a conventional wood-frame wall home. However, other construction savings greatly reduces this increase like having smaller HVAC systems or no furring out of block walls since the ICF’s are ready to accept drywall with no additional steps.
Built to last, they have greater efficiency than a conventional stick built home, more peace and quiet, a healthier living environment, low-maintenance cost, and typically are faster to build. Building with ICFs is also cost effective since it can be compared equally to a home built with 2" x 6" exterior walls, but with added benefits of more comfort and efficiency. If you have access to specialty contractors or are indifferent to installation costs, insulated concrete forms are the ideal choice for any concrete wall or foundation.
No comments:
Post a Comment